|
GENERAL INFORMATION
The hydraulically-actuated rear wheel brake is a two-shoe, double-acting, non-servo floating
type brake with an adjusting screw for each shoe. Two double piston wheel cylinders are used
in this design and are equally effective in the forward and reverse directions (Fig. 1).
On the Twinplex wheel brake assembly, the shoes anchor at either toe or heel, depending on
the direcnon of drum rotation; thus they are always forwardacting and provide equal braking
effort regardless of the direction in which the vehicle is moving. Brake anchor supports have
removable slot anchor pins and/or keys at the shoe heel, and adjusting screws at the shoe toes,
which act as anchors in the reverse direction of rotation. Each adjusting screw is threaded
into or out of its support by means of a star wheel, as required, to establish proper lining
clearance. The self—adjuster mechanism slides up a ramp and automatically maintains correct
shoe-to-drum clearance. When brakes are applied, thrust is applied equally to all four shoe
ends by the wheel cylinder pistons. Shoe contact with the drums causes the shoes to move with
the drums until the leading ends butt against the anchor brackets in forward braking or against
the adjusting pins in reverse braking. The shoe ends are free to move laterally on the angular
abutment or adjusting screw surfaces. Since lining friction tends to force the trailing ends of
the shoes into the drum, considerable added force is derived from this self-energizing action
(Figs. 1 and 2).
|
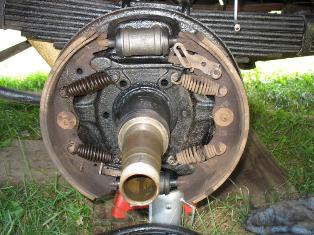
Rear Wheel Duo-Servo brake
|
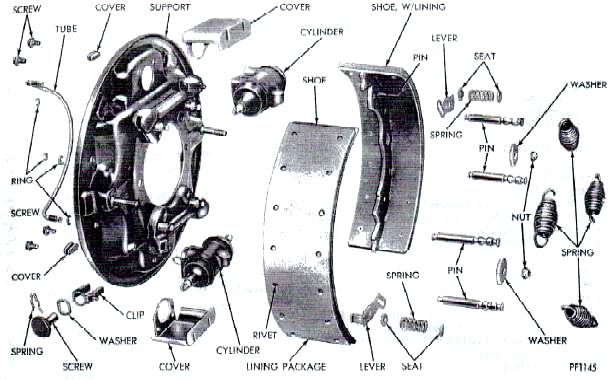
Figure 1 - Two Cylinder Floating Shoe Brake (Disassembled)
|
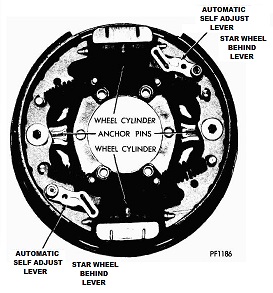
Figure 2 - Two Cylinder Hydralic Brake Assembly

Figure 2a - Upper Brake Star Adjuster
|
This brake assembly is used as follows:
- M375 models up to February 1971 have a single hydraulic system and the wheel cylinders are
interconnected (Fig. 4).
- M375 models after February 1971 have a split nydraulic system and brake actuation in split,
front/rear. Each rear wheel cylinder is fed individually.
- RM400 (M500) models use dual hydraulic system and rear wheel cylinders are interconnected.
|
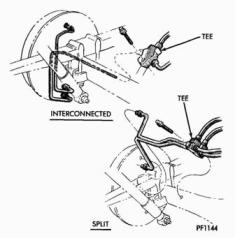
Figure 3 - Rear Wheel Brake Lines
|
SERVICE PROCEDURES
|
BRAKE SHOES
Removal
- Remove wheels and drums. Install wheel cylinder clamps to hold pistons in cylinder.
- With spring pliers slip loop ends of shoe retracting springs off anchor pin.
- Remove shoe hold down lock wires or cotter keys and castellated nuts and lift off shoes.
Anchor pins should pull out of anchor support easily.
- Dismantle adjusting mechanism. Remove adjuster lock springs by loosening their hold down
screws or snap ring out of position.
- Thread each adjusting screw from shoe side of its support.
- Lift star wheels from slot.
- Clean dirt and grease from mechanism.
- Wheel cylinders are removed by uncoupling connector tubes and removing mounting bolt.
- Mark tubing ports to avoid error in assembly. If tubes are assembled in wrong location,
diillculty may be encountered in bleeding operating.
Installation
- Install each wheel cylinder so that its long end (measured from fluid inlet port to end
of cylinder) faces toward shoe toe and adjustment slot.
- Apply a thin coat of Lubriplate to one side of hold down washer and assembly coated side
against shoe web. Place a .025 inch feeler gauge between center shoe edge and rim of shoe.
Hold shoe in position against anchor bracket and adjusting screw pad, assembly hold down
nut, and draw it down finger tight against washer. Back off one castellation (cotter pin
slot) insert cotter pin and remove feeler gauge.
For best results, new linings on shoes should be ground (not bulfed). If this is not done,
proper lining to drum contact may not be attained after normal run in.
Adjustment (lf Required)
Adjustment for lining wear is made by reducing excessive working clearance between lining
and drum. For maximum safety, manual or booster powered brake systems require adjustment when
brake pedal reserve is reduced to 2 or 3 inches, that is when the pedal drops to within 2 to 3
inches of the floor board, on a hard brake application.
- Brake adjustments may be made with the vehicle resting on jacks or on the road.
- On jacks, check brake drag by rotating drums in forward direction of rotation.
- On road, check brake drag by sound, tapping drum with adjusting wrench. A clear tone is
desired; when sound is deadened, linings are dragging on drum.
- Allow brake drums to cool olf.
- Check and adjust wheel bearings.
- Check and adjust pedal linkage on hydraulic master cylinder. If the pedal linkage does not
provide proper clearance or "lash" between the master cylinder piston and linkage with
brakes released, the piston cannot return to full "oif" position and the primary cup lip
will seal the cylinder by-pass port. Then the compensating feature of the master cylinder
cannot function and surplus fluid cannot return from the brake lines. Brakes will drag
after several applications ef the by-pass port is blocked. Adjust linkage to provide 1/8
inch free play measured at the brake medal. Greater free play will reduce the usable
stroke of the master cylinder piston.
- Check hydraulic fluid level in master cylinder. Fluid should be at least 1/4 inch below
filler cap to allow for adequate air space on all models.
- Bleed system if necessary.
- Remove brake adjustment slot covers at each wheel.
- At one adjustment slot, insert tool C-3784 or screwdriver and engage star wheel.
- Move tool handle toward axle, turning inner edge of slot at fulcrum for tool, to rotate
star wheel and decrease lining clearance until lining drags on drum.
- Press and release foot pedal to center shoe and again rotate star wheel and decrease
lining clearance until lining drags on drum.
- Relieve drag by rotating star wheel in opposite direction.
- Back off adjustment.
- At second adjustment slot insert Tool C-3784 and adjust remaining shoe.
- Replace adjustment slot covers.
|
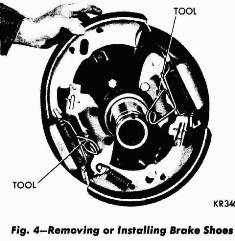
Figure 4 - Removing or Installing Brake Shoes
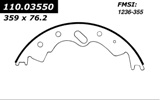
Twinplex Brake Shoe (FMSI 1236-355)
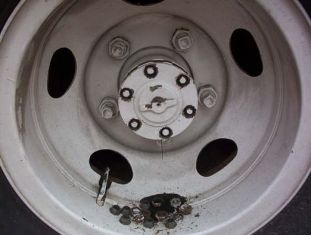
Axel Nuts, Washers, Cones Removed
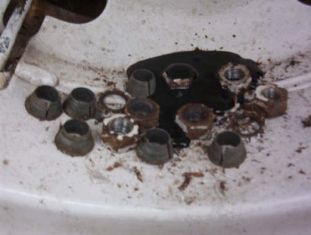
Closeup - Axel Nuts, Washers, Cones
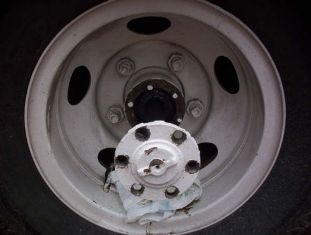
Removing Axle
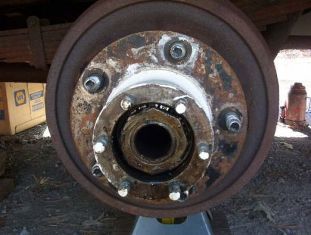
Axle Removed
|
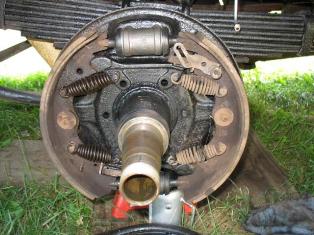
Axle and Drum Removed
|
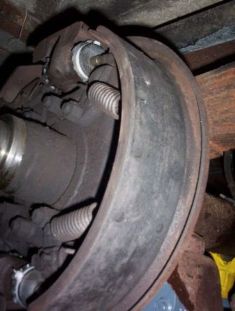
Side View of Brake Assembly
|
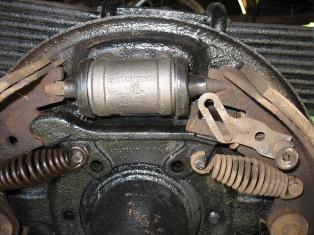
Upper Wheel Cylinder
|
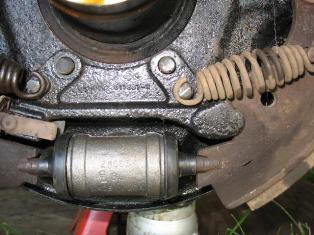
Lower Wheel Cylinder
|
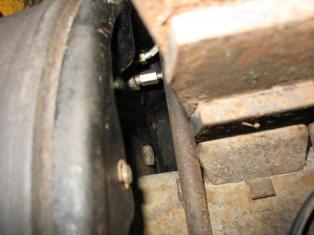
Upper Cylinder Bleeder Valve
|
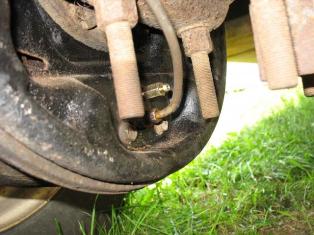
Lower Cylinder Bleeder Valve
|
|